With the rapid development of the laser welding machine market, many traditional welding processes are using hand-held laser welding machines. The laser welding machine is mainly aimed at the thin plate field. Compared with the traditional equipment, it has great advantages. It has the characteristics of high welding efficiency, good quality, and simple operation.
Early handheld laser welding machines used water cooling for heat dissipation, which is simple in structure and easy to maintain.
However, in the process of use, the market gradually found that the water-cooled hand-held laser welding machine has shortcomings in portability and functional ductility. At the same time, the characteristics of anti-freezing in winter and anti-condensing in summer also increase the difficulty of equipment maintenance.
As the market demand becomes more sophisticated, some manufacturers have begun to consider using air-cooled solutions as hand-held laser welding machines.
Compared with the water-cooled solution, the hand-held laser welding machine using the air-cooled solution does not require additional water-cooling equipment, which reduces the size and weight of the equipment, and also provides convenience for the later addition of cleaning, cutting and other functions.
Air-cooled handheld laser welding is the key to further replacing the argon arc welding market with greater cost-effectiveness and more flexible application scenarios (small size, portability, and extended functions).
Commonly used handheld laser welding machine prices in the Market
When you do a search online, you’ll come across a lot of different prices for hand held laser welders.
Some machines are priced under $1,000, but others can cost as much as $50,000.
When you go online, you get confused. If you want real results and answers, it’s best to contact the manufacturer and ask them the price of the device.
Different manufacturers Factory offer different prices. They can’t possibly have a median interest rate. A rough estimate of its cost would be around $6,000 to $15,000 for a mid-sized Handheld Laser welding machine.
High-tech and advanced handheld laser welder machines priced above $15,000 but below $25,000
Parts of a Handheld Laser Welder Machine
In order for you to fully understand a handheld laser welder Machine, you need to know its parts.
The main components of the laser welding Machine including
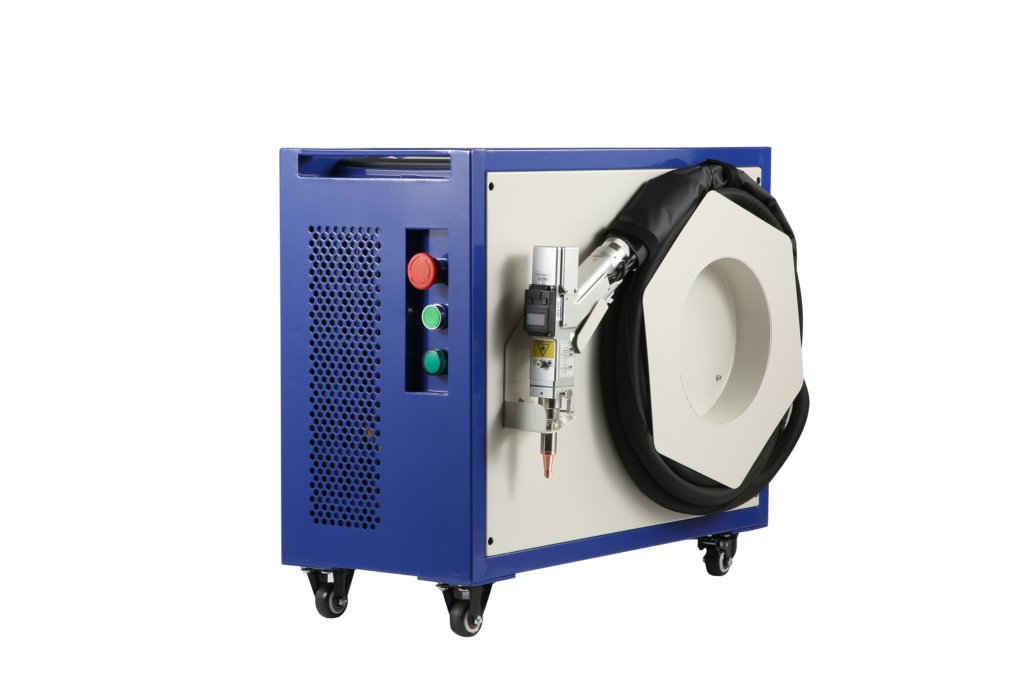
#Main control system
#Air cooled
#Machine Switch
#Screen or control system
#hand-held laser head
#Fiber Laser Source
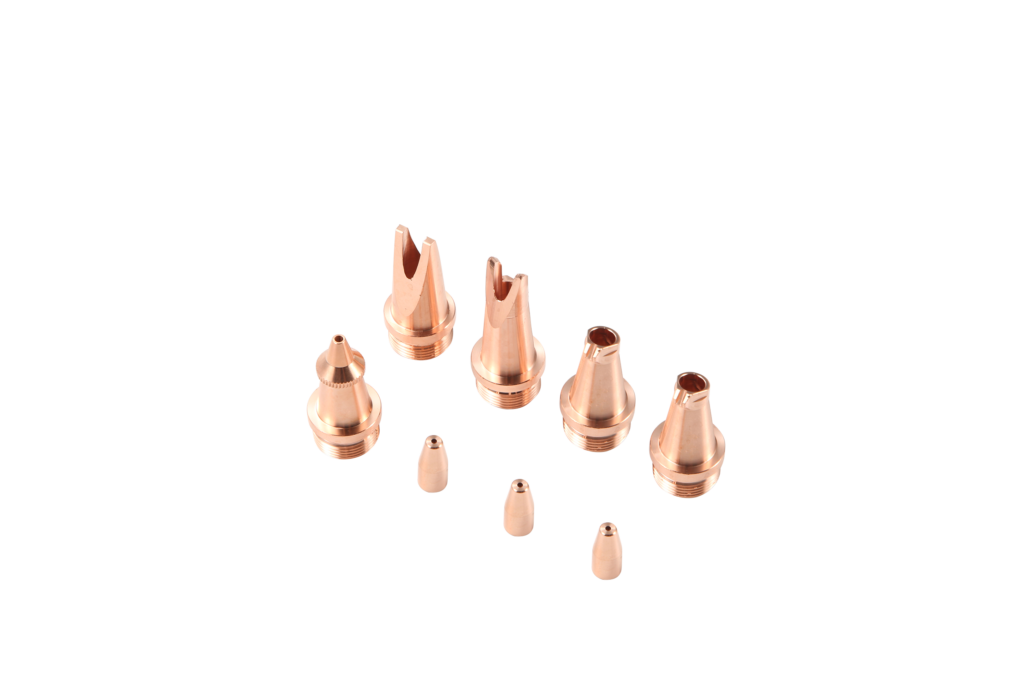
The handheld laser head consists of the following parts:
#main switch or button
#Copper Nozzle
#protective lens
#Focusing lens
#Reflector
#QBH Protective Sleeve
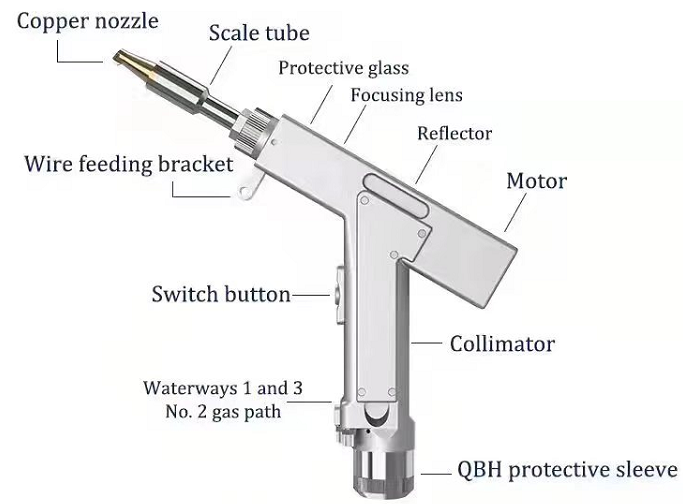
What are the advantages of Fiber Laser welding machine?
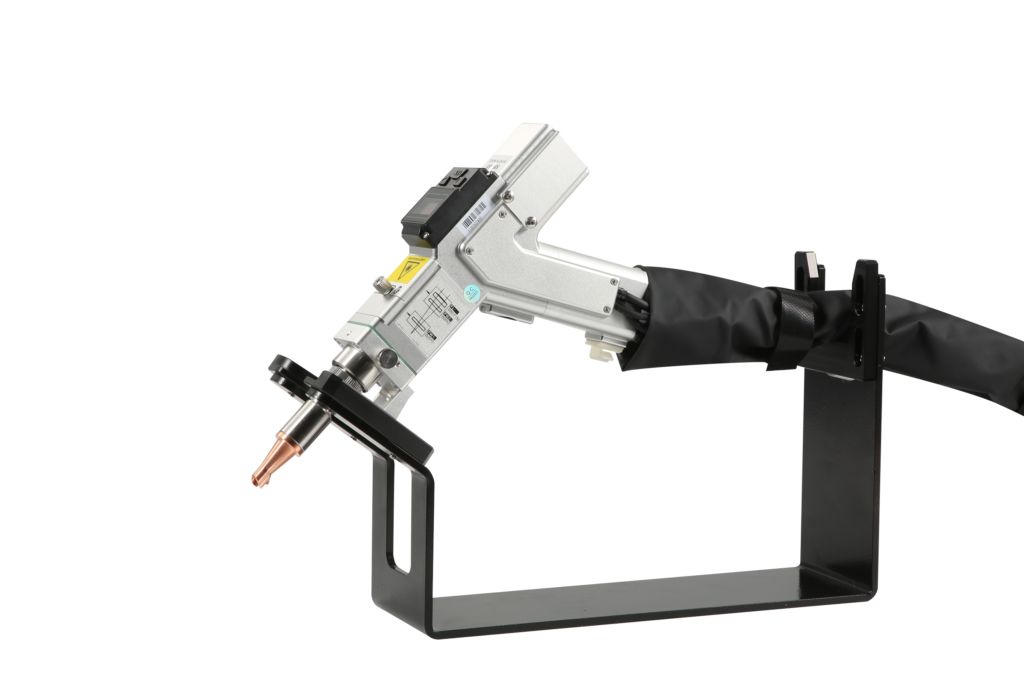
Laser welding can bring you many advantages.
The most common of these include: Highest accuracy and precision
Even if you are welding small parts and assemblies,Handheld Laser welding machine is no problem.
Welder Consistency
Because you manually set the speed, power and mode so on, you can expect that your welds will be consistent – even if you need to weld a large number of workpieces.
Combined with the fact that you can welder faster, So laser welding Machine is really your first choice
Some welding techniques, such as MIG welding and TIG welding, are not best suited for complex welding; this is due to the limited number of electrodes available.
That’s when Fiber laser welding took it up a notch. No matter how complex a weld looks, The laser welder Machine all can do it.
Stronger, more durable welds
Last but definitely not the least is the fact that you can have stronger welds.
You can welder it with filler material that requires wire or no wire, which provides excellent strength and durability.
Portability
It has a small size and is highly lightweight. As a result, this makes it useful for onsite and offsite operations. With it, you can accurately weld parts with complex designs or large parts.
Versatility
It is compatible with many material types. Additionally, it is suitable for both different and similar materials. However, for dissimilar materials, there is a need to check for material compatibility using their chemical and physical properties.
Welding Speed
Laser welding system generally has a fast welding speed due to the highly concentrated heat source. As a result, they are the better choice for production efficiency.
Heat Input
Compared to other methods, the handheld laser welder’s low heat input makes them ideal for joining thin, delicate parts. Other methods can lead to charring and dimensional inaccuracy.
Handheld laser welders also have their shortcomings, including the following:
Initial Investment
The cost of running a handheld laser system is quite high. In addition to the initial investment, the maintenance fee and labor cost contribute to the overall expenses associated with this machine.
Power Output
Compared to other methods, handheld laser welders have a relatively low power output which can be an advantage but offers disadvantages in terms of welding efficiency.
These are just some of the most Popular-after benefits of laser welding.
What Are the Common Traditional Welding Techniques and How Do They Work?
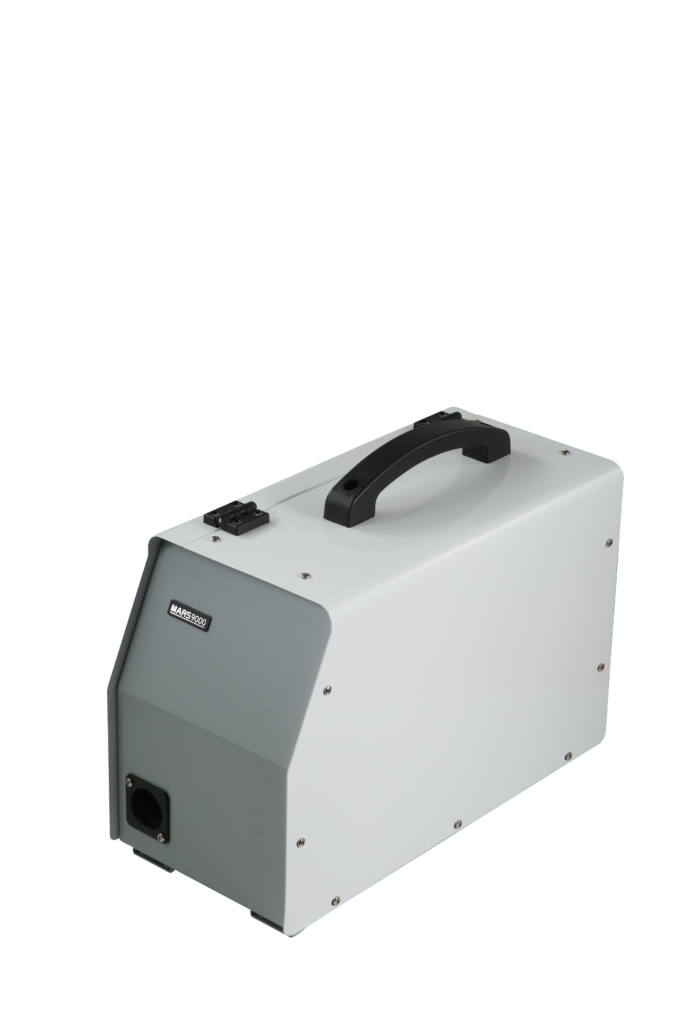
Below are the conventional welding techniques and how they work:
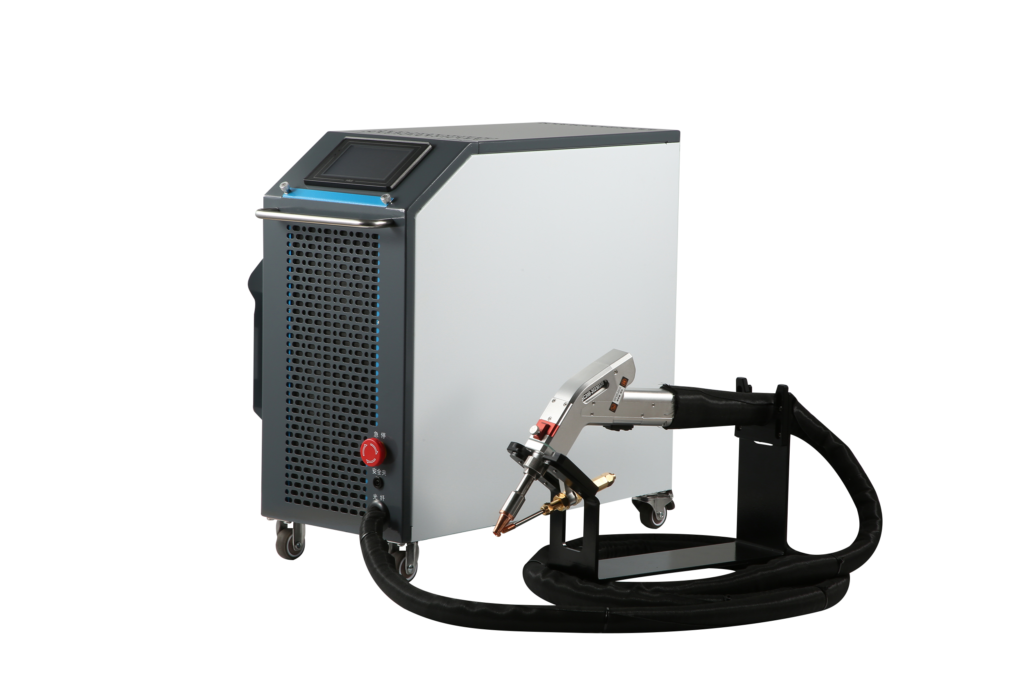
Traditional welding
· Metal Inert Gas Welding (MIG)
This welding technique welds two materials by melting a filler into the welding joint created by the adjoining piece. The direct current (power source) creates an arc, hence the welding technique’s name.
Typically, a direct current is the power source that provides the electrical energy which melts the filler material while creating an electric arc into the workpiece. On cooling, this joins the two materials.
Concurrently, an inert gas, usually argon and helium, travels through the welding head. These gases shield the weld zones from atmospheric contamination. Its efficiency and creation of uniform and clean seams make it suitable for welding parts in industries that deal with manufacturing and fabrication.
· Tungsten Inert Gas Welding (TIG)
TIG welding uses a tungsten electrode as a filler material. The filler material is unique such that it does not melt. It only supplies the heat which melts the workpiece and joins them on cooling.
TIG welding also uses shielding gas such as helium and argon. Furthermore, the created welded joint is strong. As a result, they are suitable for joining structural parts.
· Shielded Metal Arc Welding (SMAW)
This welding technique uses a flux pre-coated electrode to form the electric arc. Like MIG welding, the electrode melts the material surface while acting as a filler material, forming a weld pool. Also, the flux coatings on melting improve weld quality by eliminating the need for external shielding gas, leaving joints of high mechanical strength. The type of electrode and flux composition varies. The base material property and welding parameters affect the selection process.
· Oxyacetylene Welding (OAW)
Oxyacetylene welding uses oxygen and acetylene gases to join metals together. Acetylene gas, a combination of carbon and hydrogen, is a fuel gas. In the presence of oxygen, acetylene gas burns and produces a high-temperature flame that is hot enough to melt most metals. With the right ratio of both gases, oxyacetylene provides a flexible and efficient welding operation.
Furthermore, the oxyacetylene welding process is primarily for metals with a high melting point. However, it can also be optimized for non-metallic materials, including thermoplastics and glass. It is important to note to control the temperature as extreme heat may damage the material’s structure.
Traditional Welding Techniques: Advantages and Disadvantages
Consider TIG, MIG, and other traditional welding techniques for the following reasons:
· Operating Cost
Many of the above traditional processes are cost-effective options. The cost of operating them is low and does not significantly affect a company’s finances. The machines are affordable and do not require heavy investment to train the operators. Additionally, they are accessible and readily available for many businesses.
· Weld Strength
These processes can create more durable welds. The heat generated by the welding arc gets transferred to the base material quickly. This creates a strong bond that can withstand stress and vibrations.
· Versatility
Most conventional welding methods are versatile as they can produce temporary and permanent welds on metals, thermoplastics and glass.
· Material Thickness
The total heat input is high, which makes them suitable for thick materials.
Conventional welding has some shortcomings, which include:
· Part Deformation
Most of these conventional methods are associated with an unintended heat transfer to the surrounding material. This high heat-affected zone area deforms thin materials and parts.
· Welding Rate
The arc welding method is time-consuming. It requires multiple passes to complete a single welding operation. Additionally, most welds require post-welding grinding to remove surface irregularities.
Handheld Laser Welding Vs Traditional Welding
Maybe you want to know what are the benefits of a handheld laser welding machine?
Let’s move on to the benefits handheld laser welding machine.
better control
Control from mode, speed, power, heat, etc., control in machine motion. You can set it to the minimum or maximum value according to your Used
No electrodes required
We also know that you don’t have to use electrodes of any kind for this. Therefore, you can expect to reduce the cost and loss of output.
Easy to focus
The handheld laser welding machine laser beam you will use for welding or cutting is easy to focus.
You’ll have optics as a calibration guide, and you’ll never have to worry about quality.
Cost and Ease of Use
Handheld laser welding machines come with a relatively high investment. Additionally, the servicing and maintenance fees are also considerably more compared to the traditional methods.
Regarding ease of use, traditional methods require technical expertise, which can increase operating costs. Furthermore, handheld laser welders have easier to use. Some models even feature automation which increases operational use.
Speed and Production Efficiency
With a faster heating and cooling rate, handheld laser welders are better than traditional methods. As a result, they are more efficient and productive in terms of small-scale welding. However, in large-scale welding, traditional methods are more suitable due to the higher long life compared to laser welders.
Heat Affected Zone (HAZ)
The area around the weld joint that experiences an appreciable temperature increase also differentiates the different welding processes. The HAZ is smaller because laser welding is a contactless process that uses a focused laser beam.
On the other hand, the heat from most traditional welding techniques affects the surrounding material extensively. This can change the microstructure of the metals through recrystallization, phase transformations and precipitation. Furthermore, the area of the heat-affected zone differs among conventional welding methods. The HAZ mig welding produces comparatively larger because it has a high heat input.
Precision and Control
The control level in laser welders depends on the level of automation. Nevertheless, the operator has total control. This is better than traditional welding techniques, which have lesser precision, no automation, and require high control and focus.
Furthermore, the accuracy and precision of the final weld made with traditional methods may be lower. However, using a highly skilled operator can overcome this shortcoming. By overseeing the process, the consistency of the final weld may be similar to laser welds.
Material Compatibility
Laser welding has wide material compatibility, although it is more suitable for thin parts. The smaller heat-affected zone they produce makes them the method of choice for delicate and heat-sensitive materials.
On the other hand, the material compatibility of traditional techniques depends on the method used. Most are strictly for joining metals and may be less effective for non-metallic materials. However, traditional welding techniques are better for very thick parts because of their high heat input.
Applications
Though one uses different welding methods for manufacturing and repair operations, their application in industries differs. Handheld laser welders are more suitable for small-scale welding and materials with thin, delicate, or complex designs.
However, traditional methods, especially MiG welding, are more suitable for chassis and frames. Furthermore, arc welding has limited use in the electronics industry because it can damage electric components irreversibly.
Other benefits include:
No protection against vacuum or radiation required
can worked in a small area
Can operate in tight spaces
Conclusion
Handheld laser welding machines are becoming popular in several part manufacturing industry. They have some advantages and disadvantages over traditional welding techniques. Hence, they have variable applications. This article compared both welding systems, to inform you on choosing the right one for your project. If you have any questions, please contact us concerning the different welding methods.
Many people choose automatic laser welding machines instead of hand-held welding machines. While that’s fine, it’s better to start it manually because you’ll learn a lot from it as well.
Which handheld laser welding machine manufacturer should you choose?
In a sea of handheld laser welding machine manufacturers, comwelder Machine tops the list.
We have been leading the industry for decades, and we have never disappointed a customer with a high return rate
You can buy a lot of laser welders from us – not just Laser welding Machine. There are also several Fiber metal laser cutting machines, jewelry welding machines, jewelry cutting machines, and engraving machines.
Machine features:
High electro-optical conversion rate, energy saving and environmental protection;
High output power and superior beam quality;
High stability, high reliability, long lifetime;
Full fiber structure, compact structure, maintenance-free, low cost;
Special refrigeration scheme, air-cooled design, reduce energy consumption, and ensure stable and long term light emission;
With modular design, the weight and dimensions are much smaller than similar products in the current
The maximum power is 1500W, the penetration depth is more than 4 mm