When choosing a laser welding light source, various factors such as the welding material, joint geometry, speed, and others must be taken into account.
In the manufacturing industry, the correct selection of a laser source is a practical challenge that manufacturers must address due to the widespread use of laser welding.
Currently, the available laser sources in the market include optical fiber, pulsed Nd: YAG, diode, disc, and CO2 laser sources. (Note: The CW Nd: YAG laser source has been largely replaced by optical fiber and disc lasers, and thus is not discussed in this paper).
The choice of a laser source must consider several factors, including the welding material, joint geometry, welding speed, geometric tolerance, system integration requirements, and of course, budget constraints.
Each laser source has unique characteristics that can meet different welding requirements. In some cases, they can also be substituted.
4 Types of Laser
CO2 laser
The CO2 laser, which operates at a wavelength of 10604nm and has a power range of 1 to 20kW, is a highly developed laser technology. It has been the primary laser source for high-power processing since the 1980s.
Compared with solid-state lasers, CO2 offers a higher conversion efficiency and is capable of high-power continuous oscillation (CW, or continuous wave). The excitation source is a discharge-type source with wavelengths of 10.6 μm and 9.4 μm. Wavelengths of 10.6 μm are used for welding. Gas laser welding is used in a wide range of fields due to the ability to weld not only metal but also resin.
CO2 laser welding (carbon dioxide laser welding)
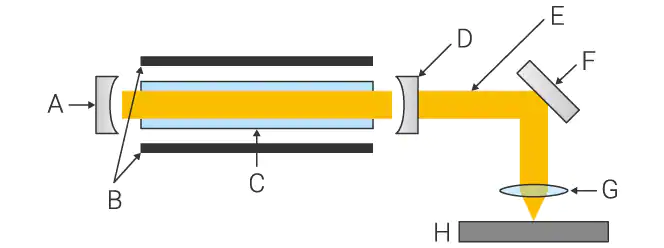
A Full reflector B Electrode C Laser gas D Partial reflector E Laser beam F Metal mirror G Lens H Workpiece
Fiber laser
This efficient diode-pumped laser uses a small core-diameter silicon-based fiber.
The laser source is housed within the optical fiber, eliminating the need for additional correction. With the small core diameter optical fiber mapped to the focusing lens, the minimum focus size can reach 10 microns.
The compact laser is available in two configurations: low power welding (less than 300W) and multi-mode for high-power welding.
Fiber lasers are one class of solid-state lasers in which the gain medium is an optical fiber. Fiber lasers have been a key technology in the area of solid-state lasers, since the first proposal of using an optical fiber as a mode selector for lasers [1]. An example of basic fiber laser configurations is shown in Figure 1.
Schematic of fiber laser
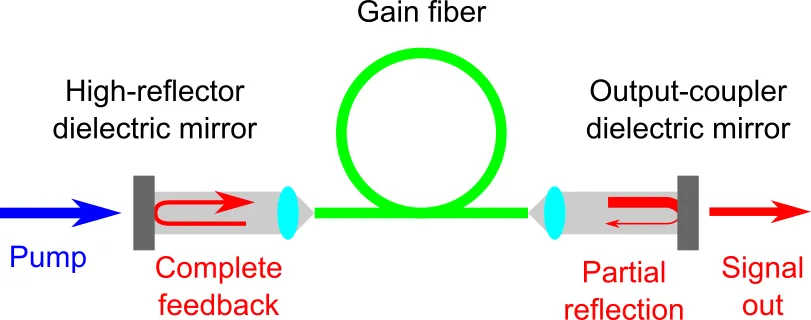
Figure 1: Schematic of fiber laser
Stimulated emissions from the gain fiber coherently amplify the signal as the signal repeatedly bounces back between the two signal reflectors. The reflector on one end of the cavity is a high reflector (ideally 100% reflectivity at the signal wavelength) in order to maximize the signal feedback to the cavity. The reflector on the other end of the cavity is a partial reflector (also called an output coupler) for extracting the signal out of the cavity, as well as providing the signal feedback to the cavity.
The output from a fiber laser can be either continuous wave (CW) or pulsed. Pulsed fiber lasers are created by modulating the loss of the laser cavity, and the pulsewidth is determined by the temporal profile of the loss modulation and the chromatic dispersion of the cavity.
Diode laser
The improvement in the power of single-surface diode laser devices, the advent of new cooling channel technology, and the advancement of micro optical element technology that can focus the beam into optical fibers with a diameter less than 1000 microns have led to the rise of diode lasers as welding sources.
A laser diode falls under the category of optoelectronics which is a branch of electronics that deals with light-emitting and light-detecting devices. A laser diode is a special LED or IRED with a relatively large and flat P-N junction.
How a Laser Diode Works
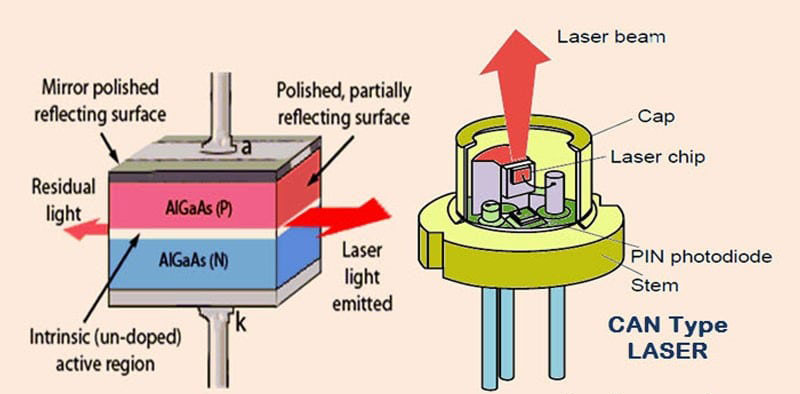
Laser diodes are light-emitting diodes with two “mirrors” on the surface of the diode to create a laser cavity.
laser diode design
The p-n junction of the diode functions as the resonant cavity of the laser. Forward bias injects charges into the junction, causing spontaneous emission of photons.
When the diode is forward-biased, charges are injected into the active area of the junction, while electrons and holes recombine in the junction, creating spontaneous emission of photons.
When this process crosses a threshold level, current passing through the diode causes it to lase – in turn creating a “laser”.
A laser includes a photodiode to sense the intensity of light emerging through the polished rear end of the laser diode. External electronics are necessary to control the intensity of the laser, using feedback from the photodiode.
Disc laser
The flat YD YAG crystal thin disk in the center of the CW laser, known as the disc laser, is designed to eliminate the inherent issues of the rod laser. A disk with a thickness of 0.01 inches is utilized and kept cool by a supporting cooling device. This design enables the laser to achieve a power output of 10 kW while maintaining excellent beam quality.
Pulsed Nd: YAG laser
This laser employs a single Nd:YAG laser rod to generate high peak power and low average power for welding through flash lamp excitation. For instance, a 35W average power laser can produce a peak power of 6kW. The combination of high peak power and a narrow pulse width not only ensures the quality of material welding, but also offers effective control over the energy input.
Select laser according to penetration size
The choice of laser can be categorized into three groups based on penetration: less than 0.01 inches, between 0.01 to 0.03 inches, and more than 0.03 inches.
Generally, multiple laser sources can be used to complete welding, however, for performance and budget reasons, only one or two light sources may be chosen.
The final decision may also be influenced by various other factors, such as the quality of the sample, geographical considerations, after-sales service, preferences of system integrators, and popularity.
Weld penetration less than 0.01in
The Pulsed Nd: YAG laser is the most commonly used laser, followed by the fiber laser. In terms of component assembly, joint shape, material, and coating, the entire welding process must be precisely controlled, making the Pulsed Nd: YAG laser the best choice.
With its high peak power, the Pulsed Nd: YAG laser can produce a welding beam with a spot size larger than 1000 microns, providing great flexibility in choosing the spot size and maximizing the process window of welding while ensuring necessary tolerances in the production environment.
The fiber laser is the only continuous-wave laser in this category, and it can produce a spot size after beam focusing of less than 25 microns, providing the high power density required for welding. However, to maintain cost competitiveness in the field of micromachining, the power of fiber lasers is generally limited to 200W, which restricts its maximum spot size and power density.
The size of the soldered joint typically does not exceed 75 microns, which is one of the biggest limitations of fiber lasers. In actual production, it is often difficult to ensure a ± 15mm error range when adjusting joints or components according to fit tolerance and superposition tolerance.
Fiber lasers are mainly used in the lap welding of thin materials with high requirements for welding joints to ensure stability. The fiber laser uses a 150mm focal length lens that can produce light spots with a diameter of less than 25 microns, providing ample processing space. With lap welding, the fiber laser can produce a weld with a penetration depth of 0.01 in or higher at a high speed, with a penetration depth of 0.004in obtainable by a 200W single-mode fiber laser at speeds up to 50 in/s.
On the other hand, the Pulsed Nd: YAG laser can meet almost all applications except for thin foil welding. Its large spot size, pulse width, and peak power range allow for adjustment and optimization to meet various welding requirements.
0.01 ~ 0.03in (0.254-0.762mm) weld penetration
The application classification of pulsed Nd: YAG laser and fiber laser is still applicable, but the range is limited. The Pulsed Nd: YAG laser is mainly used for spot welding, while fiber lasers with a power of approximately 500W and a spot diameter of 0.01 μm can be used in butt welding and fillet welding with low tolerance. The cost-performance of the Pulsed Nd: YAG laser is relatively high.
Lasers with power levels of 500W and 25W produce different weld penetration at varying welding speeds. The peak power ensures penetration performance, while the average power determines the welding speed of seam welding.
Diode lasers with power ranging between 500W and 800W are suitable for welding components with large tolerances, but the speed is generally slower than that of fiber and disc lasers. However, their large tolerance can make up for this drawback.
Weld penetration greater than 0.03in (0.762mm)
All types of lasers are suitable for this range. The penetration depth of the Pulsed Nd: YAG laser is around 0.05 in (1.27 mm), while other laser types can reach up to 0.25 in (6.35 mm) and some even exceed 0.5 in (12.5 mm).
Generally speaking, the parts suitable for Pulsed Nd: YAG laser welding in this range are relatively small, such as pressure sensors with seam welding.
The automotive industry requires a wide range of welding applications, and optical fiber, CO2, disc, and diode lasers can all be used. In terms of speed and penetration, the automotive industry covers almost all welding applications.
Seek balance
The key differences among laser sources are beam quality, brightness, and wavelength.
The beam quality refers to the laser’s focusing ability, and brightness refers to the power density in the focused beam.
For instance, the CO2 laser and fiber laser have similar beam quality, thus if other parameters are equal, they can produce light spots with the same diameter.
However, the wavelength of the fiber laser source is one-tenth that of the CO2 light source, meaning the spot diameter that it can produce is also one-tenth that of the CO2 light source. The fiber laser source also has better beam quality and brightness.
In laser welding, the beam quality and brightness directly impact the penetration depth and speed, but do not have as direct an effect on welding stability and tolerance.
Thus, it is important to find a balance between welding performance and quality, and the width of the process window. It’s worth noting that while beam quality can be reduced to meet specific needs, poor beam quality cannot be improved.
At a 0.25-inch penetration, the welding speeds of the above-mentioned lasers are quite similar. Optical fibers and discs are faster than CO2, while diodes are slower.
Welding with high-power lasers typically requires two shifts, making the cost of purchasing the laser a consideration in the selection process. While CO2 laser is widely used and familiar to many users, its single welding cost is significantly higher than that of fiber, disc, and diode lasers.
Compared to plasma and arc welding, laser welding has more advantages in welding applications requiring penetrations of more than 0.25 inches, as it can greatly reduce thermal deformation. This reduction helps maintain the geometric shape of the part, eliminating the need for reshaping. However, matching parts may cause issues at this thickness. To overcome this, a process flow of wire filling or a combination of laser welding, plasma welding, and arc welding can be used.
Conclusion
There are various types of laser sources available for laser welding, each with its unique features and suitability for specific requirements.
It is crucial for users to comprehend thoroughly which laser source can best fulfill their welding needs.
To obtain a welding system, the optimal approach is to collaborate with the system supplier, who can determine the most appropriate laser for you.
You can also reach out to various laser manufacturers and provide them with welding samples to determine the optimal solution.
When selecting a laser, it’s important to keep in mind that welding must be balanced in terms of penetration, speed, stability, accommodating the production parts and tolerance.